Retrofit da Cidade Matarazzo, na capital paulista, exigiu concretagem especial
O projeto de revitalização do complexo Matarazzo exigiu a utilização de concreto autoadensável em 100% da obra, por ele garantir impacto estrutural mínimo nas edificações tombadas
Texto: Redação AECweb/e-Construmarket
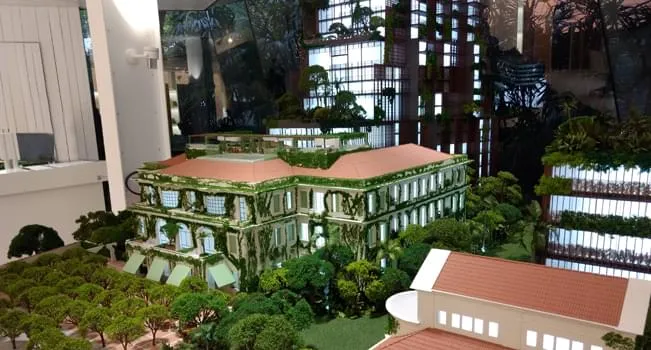
Maquete do projeto de retrofit da Cidade Matarazzo
Localizado próximo à Avenida Paulista, o complexo que abrigava o antigo hospital Matarazzo até a década de 1990 está passando por um projeto de retrofit para ser transformado em um luxuoso empreendimento. A Cidade Matarazzo, nome do novo local, contará com um hotel seis estrelas e uma área comercial de 25 mil m², além de uma extensa área verde.
Uma das principais exigências do projeto era a manutenção do patrimônio histórico e cultural tombado pelo Instituto do Patrimônio Histórico e Artístico Nacional (Iphan). Isso exigiu dos responsáveis pela obra a adoção de soluções que garantissem a integridade dos edifícios protegidos. Uma delas foi a opção pelo concreto autoadensável, cuja aplicação evita o uso de vibradores e garante o mínimo impacto estrutural possível nas edificações tombadas.
Concreto autoadensável utilizado no projeto
ESPECIFICAÇÃO DO CONCRETO
Devido à complexidade do empreendimento, o processo para a fabricação do concreto autoadensável durou mais de 12 meses de estudos e testes. Ricardo Soares, gerente geral da divisão de concreto da Votorantim Cimentos, ressaltou que o concreto utilizado na obra apresenta características distintas do convencional. “Normalmente, os concretos utilizados no Brasil apresentam resistência entre 20 e 30 MPa. O cliente solicitou para essa obra uma resistência altíssima, de 60 Mpa.”
Normalmente, os concretos utilizados no Brasil apresentam resistência entre 20 e 30 MPa. O cliente solicitou para essa obra uma resistência altíssima, de 60 MpaRicardo Soares
TESTES
Além da resistência, era necessário alcançar um acabamento perfeito após a desforma – liso, sem bolhas e fissuras –, uma vez que a aplicação ficaria aparente. A solução foi utilizar tubos cilíndricos de acrílico de aproximadamente 1 metro de altura para verificar a reação do desmoldante com o concreto.
O tubo recebeu a aplicação do desmoldante na parte interna das paredes, sendo posteriormente preenchido com o concreto autoadensável. Dessa maneira, foi possível observar como as bolhas se dissipavam e se haveria a formação de fissuras de acordo com cada desmoldante testado.
O projeto também exigiu um concreto com uma tonalidade mais escura que a do convencional, utilizando pigmentos pretos na mistura. A medida demandou estudos sobre a reação química entre o pigmento – com alta carga magnética – e os aditivos, em especial o superplastificante.
Para encontrar a composição ideal, foi necessária a fabricação de mais de 70 traços diferentes. “Foram feitos testes com diferentes pigmentos, aditivos e componentes”, ressalta Soares.
Após a escolha do traço e do desmoldante, foi realizada a construção de um projeto teste. “Fizemos protótipos – parte de um apartamento em tamanho real – para verificar a tonalidade e o acabamento do concreto, e o resultado foi bastante satisfatório”, afirma Soares. Representantes do cliente vieram até o Brasil para avaliar diversos aspectos do protótipo, como acabamento, coloração e resistência.
CONCRETAGEM
A concretagem está sendo dividida em duas partes: a aparente e a interna. Na aparente o concreto usado é o pigmentado; como ficará exposto, exige maior cuidado no acabamento. Já a concretagem interna apresenta as mesmas propriedades, com exceção dos materiais envolvidos na pigmentação.
Além das especificidades do concreto autoadensável, o impacto do tráfego no local também impôs dificuldades à execução. Por ser uma área residencial, altamente movimentada e com bastante sinuosidade, não é possível carregar 100% da carga da betoneira.
“O caminhão não pode vir com 8 m³ por causa das inclinações das ruas. O máximo que conseguimos transportar é 7 m³. Então, o segredo é encontrar um meio termo. Não é possível trazer muitos caminhões simultaneamente, pois o acúmulo de veículos estacionados pode travar o trânsito e danificar o concreto. Mas, por outro lado, não é possível trazer poucos caminhões, pois correríamos o risco de o concreto acabar e parar a concretagem”, conta Soares.
O caminhão não pode vir com 8 m³ por causa das inclinações das ruas. O máximo que conseguimos transportar é 7 m³Ricardo Soares
Segundo ele, nas lajes de 500 m³ – as primeiras que foram realizadas –, foi necessário o abastecimento de 70 a 80 betoneiras em um único dia.
As formas também precisam de atenção especial. Pela fluidez do material, é necessário cuidar da vedação das peças. A busca pela perfeição no acabamento também exige uma forma nova para cada execução do concreto arquitetônico, enquanto que na concretagem interna a mesma forma pode ser reutilizada até 10 vezes.
O concreto é bombeado até um mastro vertical que o lança por toda a extensão da laje. Por ser autoadensável, não é necessário o uso de vibradores ou operários atuando no espalhamento do material. A cura necessita de até 7 dias e exige o uso de água para manter a umidade e gelo para reduzir o calor de hidratação, especialmente nas peças de maior porte. Até o final da obra, deverão ser utilizados 45 mil m³ de concreto.
PATRIMÔNIO TOMBADO![]()
Uma das principais preocupações desse projeto de retrofit era a manutenção do seu valor histórico e cultural. Os prédios da capela de Santa Luzia e da maternidade Condessa Filomena Matarazzo – edifícios tombados pelo Iphan – foram restaurados e mantiveram suas identidades visuais conforme o projeto original.
Durante as obras, a capela chegou a ficar elevada a uma altura de 31 metros em relação ao solo, sendo sustentada por oito pilastras de concreto para a construção do prédio comercial e de um estacionamento que ficará abaixo da estrutura.
Leia também:
Concreto autoadensável aumenta produtividade no canteiro
Retrofit moderniza edifícios e preserva patrimônio histórico
Colaboração técnica
- Ricardo Soares – É gerente geral de Concreto da Votorantim Cimentos. O executivo é responsável pela divisão de Concreto da empresa no Brasil, respondendo pela operação, distribuição, controle de qualidade e atendimento a clientes da marca Engemix. Em 13 anos de atuação na companhia, Soares já atuou em diversas áreas dentro da unidade de concreto, marketing e logística. Antes do mercado construção, trabalhou em empresas do mercado financeiro, como Banco Safra e Banco Real. É formado em Ciências Econômicas pela Universidade Federal de Minas Gerais (UFMG), possui MBA Executivo em Finanças pelo (IBMEC/SP) e mestrado em Administração de Empresas com Ênfase em Finanças pela Fundação Getúlio Vargas (FGV/SP).